Understanding Silicone Membrane for Vacuum Forming
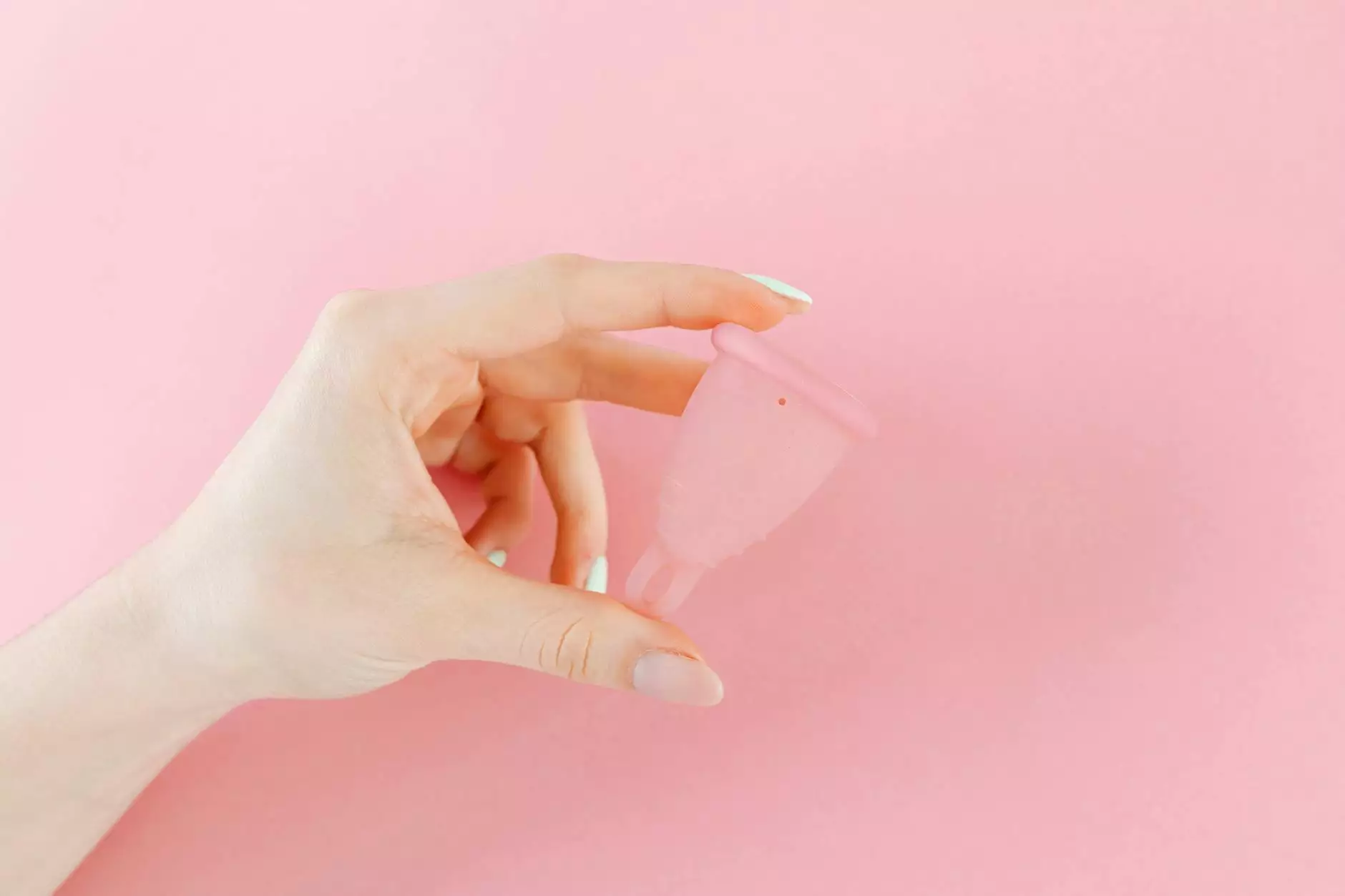
What is Vacuum Forming?
Vacuum forming is a manufacturing process that uses heat and vacuum to mold plastic sheets into specific shapes. This process is widely used in various industries including packaging, automotive, electronics, and product design. It allows for the quick production of high-quality items that meet precise specifications.
The Role of Silicone Membrane in Vacuum Forming
At the core of the vacuum forming process lies the silicone membrane, a critical component that ensures the quality and consistency of the formed parts. The silicone membrane for vacuum forming provides several benefits that enhance the efficiency and effectiveness of the manufacturing process.
Benefits of Using Silicone Membrane for Vacuum Forming
- Flexibility: Silicone membranes are incredibly flexible, allowing them to conform to various shapes and contours during the forming process.
- Durability: These membranes can withstand high temperatures and pressures, making them suitable for the demands of vacuum forming.
- Chemical Resistance: Silicone materials exhibit excellent resistance to various chemicals, ensuring they maintain integrity throughout the forming process.
- Long Lifespan: With proper care, silicone membranes can last significantly longer than other materials, reducing the need for frequent replacements.
- Better Release Properties: Silicone provides excellent release characteristics, minimizing the risk of damage to the formed parts.
Applications of Silicone Membranes
Silicone membranes are used in various applications across different sectors. Here are some notable examples:
1. Packaging Industry
In the packaging industry, silicone membranes are utilized for creating thermoformed blister packs and trays that securely hold products while ensuring visibility and accessibility.
2. Automotive Sector
The automotive industry benefits from these membranes by producing parts like dashboards and interior panels, allowing for intricate designs that enhance vehicle aesthetics and functionality.
3. Medical Devices
Silicone membranes serve in the medical field by forming components for devices that require sterilization and high precision, meeting strict regulatory standards.
4. Consumer Electronics
In electronics, silicone is used to create housings and protective casings that withstand wear and provide excellent thermal stability.
Choosing the Right Silicone Membrane
Selecting the appropriate silicone membrane for vacuum forming is crucial for the success of any project. Here are key factors to consider:
1. Thickness and Shore Hardness
The thickness of the membrane affects its performance; thinner membranes can create intricate designs while thicker options offer better durability. Consider the Shore hardness level, as this directly impacts the flexibility and firmness of the membrane.
2. Temperature Resistance
Different applications may expose the membrane to varying temperatures. Ensure that the chosen silicone can withstand such conditions without compromising its structural integrity.
3. Chemical Compatibility
Matching the chemical resistance of the silicone membrane with the materials being used in the mold is essential to avoid degradation during the forming process.
Maintenance Tips for Silicone Membranes
To extend the lifespan of your silicone membrane for vacuum forming, consider the following maintenance tips:
- Cleaning: Regularly clean the membrane using mild detergents and soft cloths to remove any residue and prevent buildup.
- Storage: Store silicone membranes in a cool, dry place away from direct sunlight to prevent deterioration.
- Avoid Sharp Objects: Ensure that sharp objects do not come into contact with the membrane during use or cleaning to prevent damage.
- Inspect Regularly: Check for any signs of wear or cracks and replace the membrane if necessary to maintain quality.
The Future of Silicone Membranes in Vacuum Forming
As technology advances, the future of silicone membranes for vacuum forming looks promising. Innovations in material science continue to enhance the properties of silicone, making it even more versatile for industrial applications. Developments such as:
- Enhanced Biocompatibility: This is critical for the medical applications of silicone membranes, ensuring safety and performance.
- Eco-Friendly Alternatives: Research into sustainable materials may lead to eco-friendly silicone solutions, reducing environmental impact.
- Smart Membranes: Integration of sensors into silicone membranes can lead to innovative applications in smart manufacturing and automation.
For those interested in purchasing high-quality silicone membranes and other vacuum system parts, visit vacuum-presses.com. We offer a wide range of products including rubber membranes and natural rubber membranes, ensuring you have everything you need for efficient vacuum forming.