Exploring Roc Welding: The Future of Precision Manufacturing
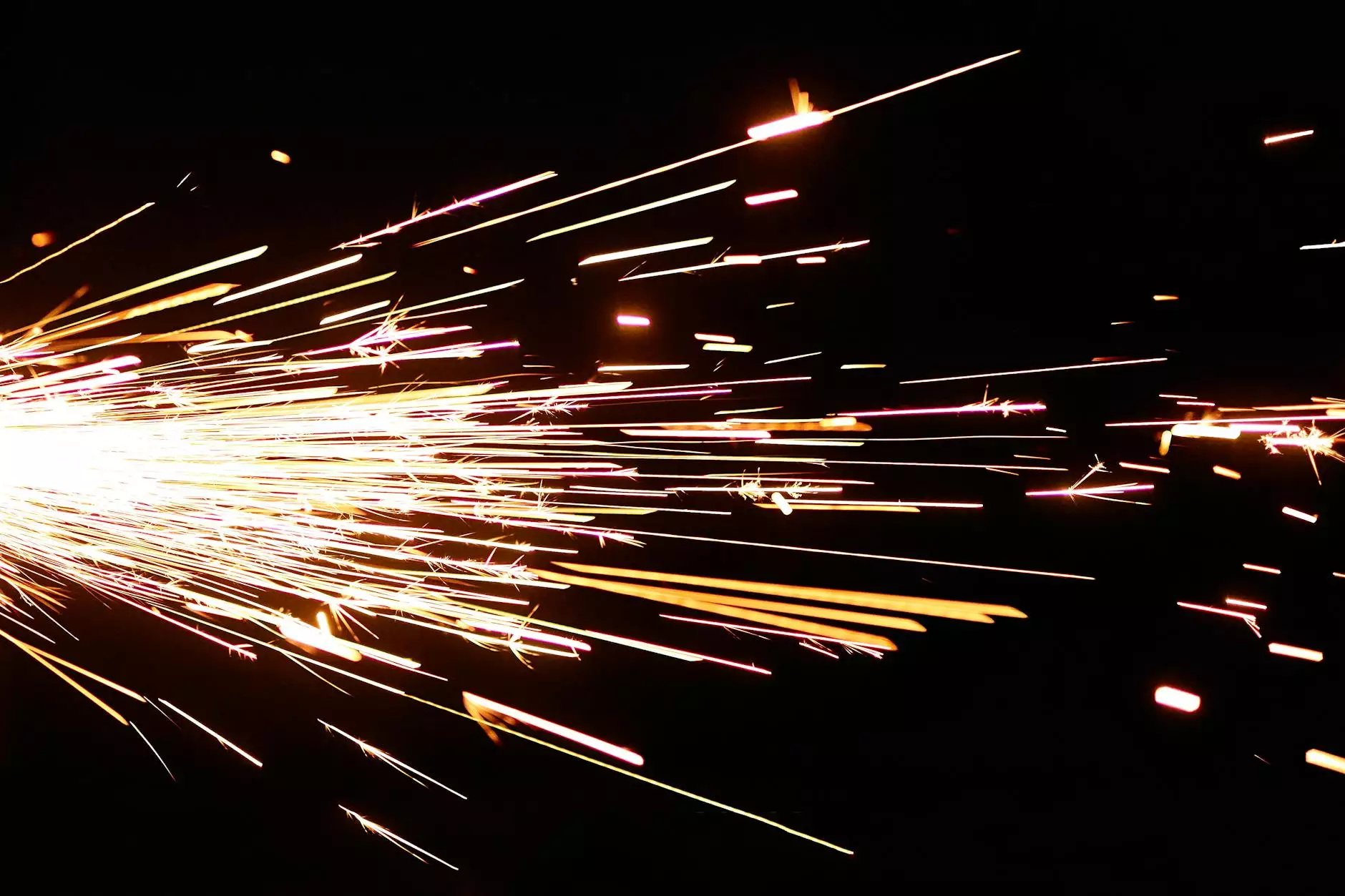
Understanding Roc Welding
Roc welding is an emerging term in the world of manufacturing that combines sophisticated welding techniques with cutting-edge technology. This innovative approach allows businesses to achieve precision and efficiency that was once thought impossible. By focusing on advancements in welding technology, including robotic welding and laser cutting machines, roc welding is set to revolutionize the manufacturing landscape.
The Importance of Welding in Modern Manufacturing
Welding is a critical process in various industries, including automotive, aerospace, and construction. It involves joining materials, typically metals, to create strong and resilient structures. The importance of welding cannot be overstated: it ensures not only the strength of products but also their longevity and durability.
The Evolution of Welding Techniques
The world of welding has evolved significantly over the years. Traditional methods have given way to modern innovations that streamline processes, improve safety, and reduce costs.
- Manual Welding: Requires skilled labor but can be time-consuming and less precise.
- Automated Welding: Introduces machines to assist with welding processes, improving speed and consistency.
- Robotic Welding: Utilizes programmed robots to execute welding tasks with incredible accuracy.
- Laser Welding: A technique that uses concentrated laser beams to melt and fuse materials at a molecular level.
What Makes Roc Welding Unique?
Roc welding differentiates itself through several key attributes:
- Increased Precision: By integrating advanced technology, roc welding techniques offer unparalleled precision and accuracy that manual methods cannot match.
- Enhanced Consistency: Automation through robotic systems ensures that every weld is consistent, minimizing variability and defects.
- Cost Efficiency: Reduced labor costs and material waste through precise welding significantly lower production costs.
- Flexibility and Scalability: Roc welding technologies can easily adapt to different production scales, making them ideal for both small and large manufacturing operations.
Integrating Laser Cutting Machines with Roc Welding
Incorporating laser cutting machines into the roc welding process enhances efficiency further.
How Laser Cutting Improves Welding
Laser cutting machines perform intricate cuts with high precision, preparing materials for seamless welding. Here’s how they support the welding process:
- Precision Cuts: Laser cutting provides clean and precise edges that are essential for strong welds.
- Reduced Material Waste: High accuracy reduces scrap material, leading to more economical production processes.
- Improved Joint Quality: Well-prepared edges enhance the quality of the weld and reduce the likelihood of defects.
Applications of Roc Welding and Laser Cutting Machines
The combination of roc welding and laser cutting machines has a wide range of applications across various industries. These include:
- Automotive Industry: Producing stronger and lighter vehicles with superior safety features.
- Aerospace Manufacturing: Building lightweight components that meet stringent safety and performance standards.
- Construction: Creating durable steel beams and components for buildings and infrastructure.
The Future of Roc Welding
The future of roc welding looks promising, driven by continuous technological advancements. As industries evolve, so too will the need for more innovative and efficient welding solutions.
Emerging Trends in Roc Welding
Some trends to watch in the welding industry include:
- Artificial Intelligence: AI systems are being integrated to optimize welding paths and parameters, further enhancing precision.
- Augmented Reality: AR applications are helping welders visualize complex components and improve training.
- Sustainability Practices: As industries shift towards greener production methods, roc welding will adapt to minimize energy usage and material waste.
Choosing the Right Equipment for Roc Welding
To excel in roc welding, businesses must invest in the right equipment. The choice of welding machines often depends on the specific applications and requirements.
Key Considerations for Equipment Selection
- Type of Materials: Different materials may require distinct welding techniques and equipment.
- Production Volume: High-volume production may benefit from automated or robotic systems.
- Precision Needs: Industries requiring high precision should consider laser welding machines for their accuracy.
Conclusion: The Transformative Power of Roc Welding
In conclusion, roc welding represents a significant advancement in the manufacturing sector, driven by precision and efficiency. By embracing technologies such as robotic welding and laser cutting machines, businesses can enhance product quality and operational efficiency. The future indicates a seamless transition towards more innovative approaches to welding, positioning roc welding as a fundamental component of modern manufacturing.
As we advance into a new era of technology and manufacturing, understanding and implementing roc welding effectively will be crucial for businesses aiming to compete on a global scale. The integration of these cutting-edge methods not only boosts operational performance but also nurtures sustainable practices, ensuring long-term success in an ever-evolving market environment.