The Comprehensive Guide to Automatic Label Applicators
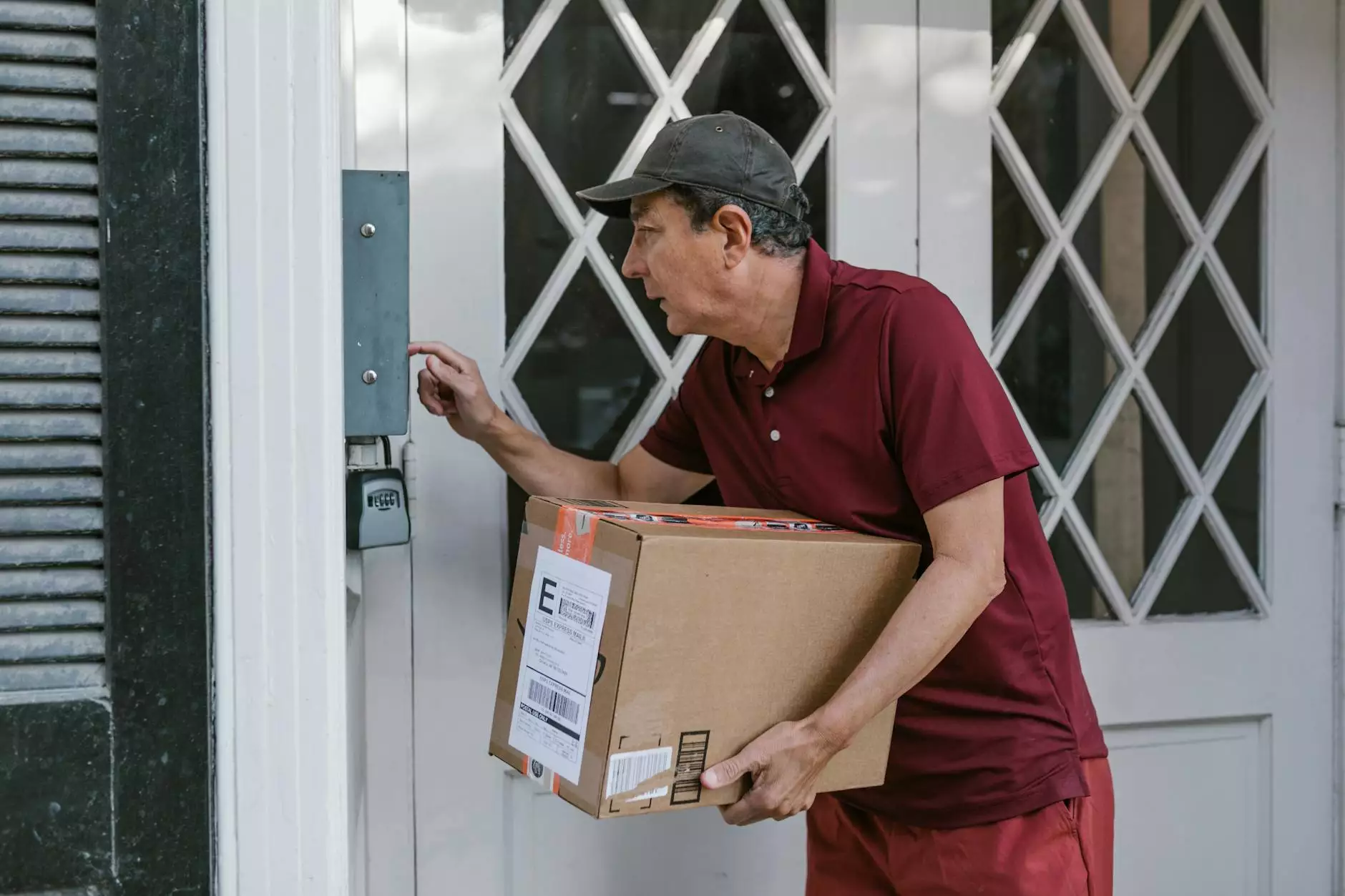
In the fast-paced world of commerce and industry, the process of labeling products plays a crucial role in ensuring efficient operations and compliance with regulations. At omegabrand.com, we understand the importance of precision in every aspect of business, especially when it comes to automatic label applicators. This guide will explore the different applications, benefits, and advancements in this technology, aiming to provide you with a thorough understanding of how these tools can enhance your business operations.
What Are Automatic Label Applicators?
Automatic label applicators are devices designed to apply labels to products in a streamlined, efficient manner. They play a pivotal role in manufacturing and packaging processes across various industries, ensuring that labeling is consistent, accurate, and high-speed. By automating the labeling process, businesses can significantly enhance productivity while reducing the labor costs associated with manual labeling.
How Do Automatic Label Applicators Work?
The functionality of automatic label applicators typically involves three primary components: a label dispenser, a product sensor, and an applicator mechanism. Below is an overview of how these elements work together:
- Label Dispenser: The machine pulls labels from a roll or sheet and prepares them for application. Labels can be sent to the applicator head either individually or as part of a continuous feed.
- Product Sensor: This component detects when a product is in position for labeling, ensuring that labels are applied at the right moment, minimizing waste and errors.
- Applicator Mechanism: Depending on the type of applicator, this mechanism applies the label. Various technologies such as tamp-blow, direct-apply, and wipe-on are used, each designed for specific applications.
Types of Automatic Label Applicators
Choosing the right type of automatic label applicator depends on your specific needs and the nature of the products you are labeling. Here are some common types:
1. Tamp-Blow Label Applicators
Tamp-blow applicators are versatile and ideal for applying labels to uneven surfaces or products with different heights. They work by extending a tamp pad to make contact with the product and then releasing the label from the pad.
2. Wipe-On Label Applicators
This type utilizes a roller that wipes the label onto the product surface. Wipe-on applicators are commonly used in industries where the labels need to be applied quickly and efficiently, such as in carton packaging.
3. Direct-Apply Label Applicators
Direct-apply machines place labels directly onto products as they pass through the machine. This method is particularly effective for high-speed production lines with uniform products.
Benefits of Using Automatic Label Applicators
The incorporation of automatic label applicators can provide numerous advantages, enhancing operational efficiency and product presentation. Key benefits include:
- Increased Efficiency: Automation significantly speeds up the labeling process, allowing for higher production rates compared to manual labeling.
- Consistency and Accuracy: Automated systems reduce the potential for human error, ensuring that labels are applied consistently and correctly every time.
- Cost-Effective: Over time, an automatic label applicator can reduce labor costs and increase output, leading to better profit margins.
- Flexibility: Many systems can be adjusted to handle different label sizes, shapes, and application methods, making them versatile for various products.
- Improved Safety: By minimizing manual handling, automatic applicators reduce the risk of workplace accidents related to repetitive tasks.
Applications of Automatic Label Applicators
Automatic label applicators are utilized across a myriad of industries, each benefiting from the efficiency and reliability these machines provide. Some key applications include:
1. Food and Beverage Industry
In the food sector, accurate labeling is critical for compliance with health regulations. Automatic label applicators ensure that expiration dates, nutritional information, and barcodes are printed and applied precisely to each product.
2. Pharmaceutical Industry
Pharmaceutical products require meticulous labeling due to stringent regulations. Automatic label applicators help in ensuring that labels with crucial information such as dosage instructions and lot numbers are applied consistently and correctly.
3. Electronics Sector
In the electronics industry, labels may include important details such as model numbers and safety information. The quick labeling of various components speeds up the production process while maintaining quality.
4. E-commerce and Retail
With the rise of e-commerce, products are shipped with labels containing tracking information, pricing, and barcodes. Automation in labeling ensures efficient processing and fulfillment in warehouses.
Choosing the Right Automatic Label Applicator
Selecting the appropriate automatic label applicator requires careful consideration of several factors:
- Production Volume: Assess the required output per hour and choose a machine that can meet or exceed those demands.
- Label Specifications: Determine the size, shape, and material of the labels you will be using and ensure the applicator is compatible.
- Product Characteristics: Consider the surface and shape of the products to be labeled. Certain applicators are better suited for uneven surfaces than others.
- Budget: Establish a budget that includes the cost of the machine, maintenance expenses, and potential savings from increased efficiency.
Maintenance Tips for Automatic Label Applicators
To ensure your automatic label applicator operates at peak efficiency, regular maintenance is essential. Consider the following tips:
- Regular Cleaning: Dust and residue can accumulate on your machine, affecting performance. Clean it regularly to keep it in optimal condition.
- Check Sensors: Regularly inspect product sensors for misalignment or blockages that could disrupt the labeling process.
- Review Settings: Ensure that the settings for label size and application speed are suited to your specific production needs.
- Scheduled Servicing: Implement a scheduled service plan with your supplier to prevent unexpected breakdowns and prolong the equipment's life.
The Future of Automatic Label Applicators
The landscape of labeling technology is continually evolving, with advancements that promise greater efficiency and integration with other technologies. Future trends include:
- Smart Technology: Integration with IoT (Internet of Things) for real-time monitoring and control of labeling processes.
- Label Printing Innovations: Advancements in printing technology that allow for on-demand label creation, reducing waste and enhancing customization.
- Enhanced User Interfaces: More intuitive control panels that make it easier for operators to adjust settings and troubleshoot issues.
Conclusion
Investing in automatic label applicators is not merely about streamlining labeling processes; it’s about embracing the future of efficiency and quality in various industries including printing services, electronics, and computers. With enhanced performance and precision, these tools represent a significant step toward modernizing business practices. Explore the options available at omegabrand.com today and transform your labeling processes for better productivity, cost savings, and high-quality output.