Understanding Automotive Mold Manufacturers
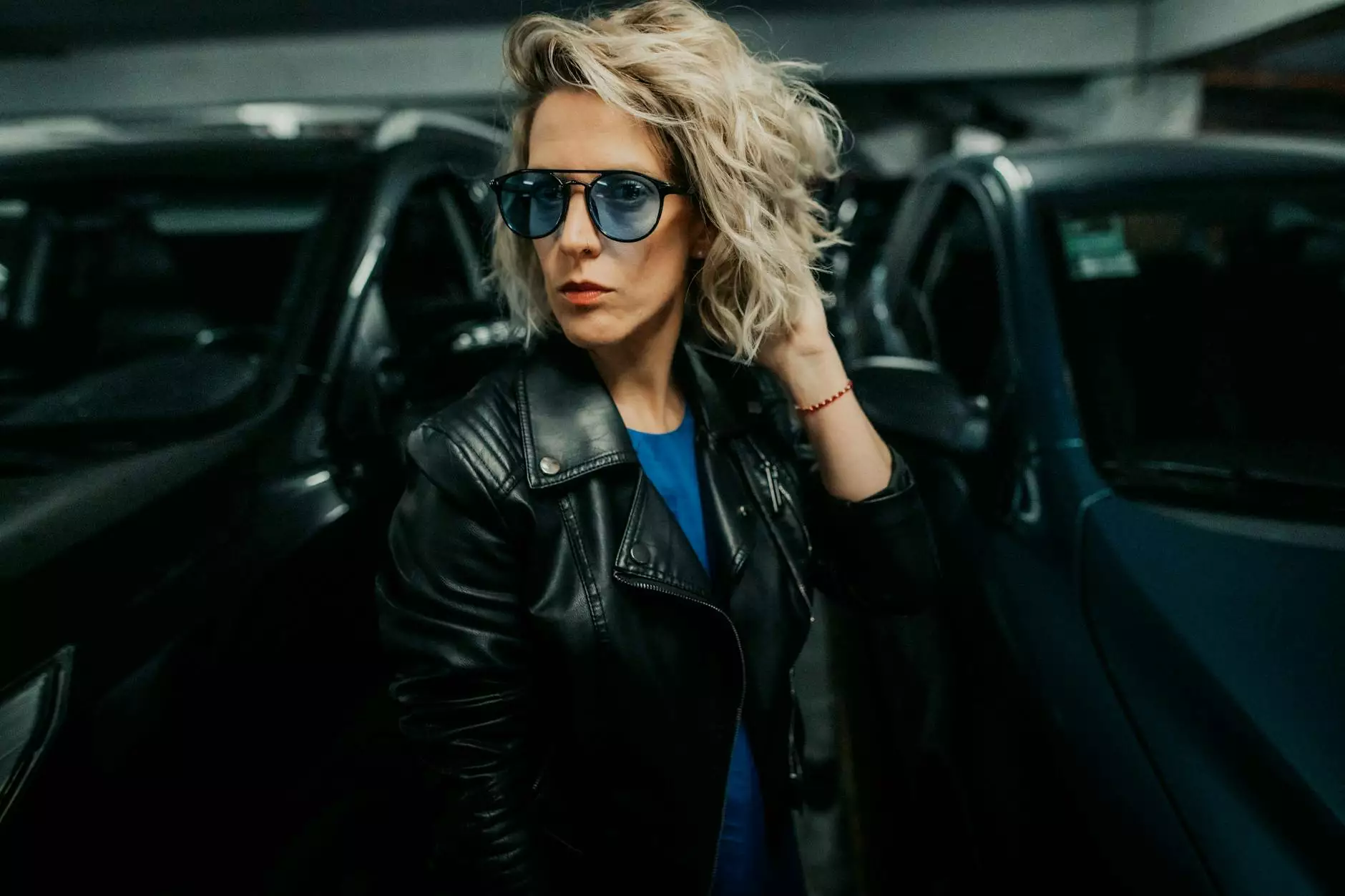
The automotive industry is a dynamic field that necessitates precision and innovation, especially in the production of vehicle components. At the heart of many of these production processes are automotive mold manufacturers, who play a crucial role in shaping the future of vehicle design and manufacturing.
What are Automotive Molds?
Automotive molds are the backbone of producing parts for vehicles, providing the essential shapes and forms necessary for assembly. These molds are crafted from durable materials and are designed to withstand the stress of repeated use in high-volume production settings.
Importance of Automotive Mold Manufacturers
Automotive mold manufacturers are pivotal in the production of various automotive components. Here are some key reasons why they are vital:
- Precision Engineering: Automotive molds are created with unparalleled precision to ensure that each part fits flawlessly into the assembly line.
- Cost Efficiency: By employing advanced manufacturing techniques, these manufacturers help minimize waste and reduce production costs.
- Quality Control: They implement stringent quality checks to ensure every molded part meets the industry standards and regulations.
- Innovation: The industry is constantly evolving, and automotive mold manufacturers are at the forefront of new technologies and materials.
The Process of Manufacturing Automotive Molds
Design and Prototyping
The journey begins with the design of the mold itself. This involves a series of steps:
- Conceptualization: Designers create initial sketches and models based on the specifications provided by car manufacturers.
- CAD Modeling: Utilizing advanced computer-aided design (CAD) software, designers turn sketches into detailed 3D models that showcase every aspect of the mold.
- Prototyping: A physical prototype is produced to test and refine the mold design before final production.
Material Selection
Selecting the right materials is crucial for the durability and efficiency of the mold. Common materials include:
- Steel: Known for its strength and longevity, steel is often used for high-volume production molds.
- Aluminum: Lighter than steel, aluminum molds are ideal for low to medium production runs.
- Composite Materials: Increasingly being used for their reduced weight and increased durability.
Mold Fabrication
Once the design and materials are finalized, the actual fabrication of the molds takes place. This includes:
The combination of CNC machining, EDM (Electrical Discharge Machining), and traditional machining techniques ensures that molds are produced to exact specifications.
Testing and Quality Assurance
After fabrication, the molds undergo rigorous testing to ensure they meet all performance requirements. Quality assurance processes are vital to ensure:
- Consistent dimensional accuracy.
- Durability under production conditions.
- Compliance with industry standards and environmental regulations.
Types of Molds Used in the Automotive Industry
Automotive mold manufacturers produce a wide array of molds, each designed for specific functions:
Injection Molds
Injection molding is one of the most commonly used methods in the automotive sector. These molds are designed to inject molten plastic into the mold cavity, which solidifies into the desired shape.
Compression Molds
Compression molds are utilized for producing parts from rubber and various thermosetting plastics. The process involves placing material in a heated mold cavity, which then compresses to form a part.
Blow Molds
Blow molding is typically used for making hollow parts, such as fuel tanks and air ducts. These molds allow for the creation of lightweight, complex shapes essential in modern vehicle design.
Benefits of Choosing Quality Automotive Mold Manufacturers
In a competitive market, selecting expert automotive mold manufacturers can yield remarkable benefits:
- Enhanced Product Quality: High-quality molds result in superior parts with fewer defects.
- Reduced Production Times: Efficient manufacturing processes enable faster turnarounds, essential for meeting market demands.
- Greater Design Flexibility: Experienced manufacturers can accommodate complex designs, allowing for innovation in vehicle production.
Challenges Faced by Automotive Mold Manufacturers
While the future looks bright for the automotive mold manufacturing sector, several challenges persist:
- Technological Advancement: Keeping up with rapid technological changes and integrating new systems can be daunting.
- Global Competition: Increased competition from international firms requires companies to remain innovative and cost-effective.
- Sustainability Concerns: There is a growing demand for environmentally friendly manufacturing practices which can require significant changes in processes.
Future Trends in Automotive Mold Manufacturing
Looking ahead, several emerging trends promise to reshape the landscape of automotive mold manufacturing:
Increased Automation
As Industry 4.0 continues to evolve, automation in mold manufacturing is set to improve efficiency. Robotics and AI-driven systems can optimize production processes and reduce labor costs.
3D Printing Technology
3D printing is progressively being utilized for creating molds, allowing for rapid prototyping and reduced material waste. This technology promises to revolutionize the design and production phases.
Green Manufacturing Practices
Sustainability will be a primary focus in the coming years, leading to the adoption of green technologies and practices to reduce carbon footprints.
Conclusion
Automotive mold manufacturers are essential players in the automotive industry, providing the necessary tools to create high-quality components. Companies like DeepMould.Net stand out with their commitment to excellence in mold fabrication, ensuring that they meet the evolving demands of the automotive sector. By understanding the importance of this niche and the innovations it entails, businesses can make informed decision to leverage these manufacturers in their production processes.
As the automotive landscape continues to evolve, the role of automotive mold manufacturers remains pivotal, paving the way for future innovations in vehicle design and manufacturing efficiency. Embracing these trends and understanding the intricacies of the manufacturing process will ensure companies can thrive in a competitive market.